Exploring the Benefits of GRP Composite Housings in Modern Industry
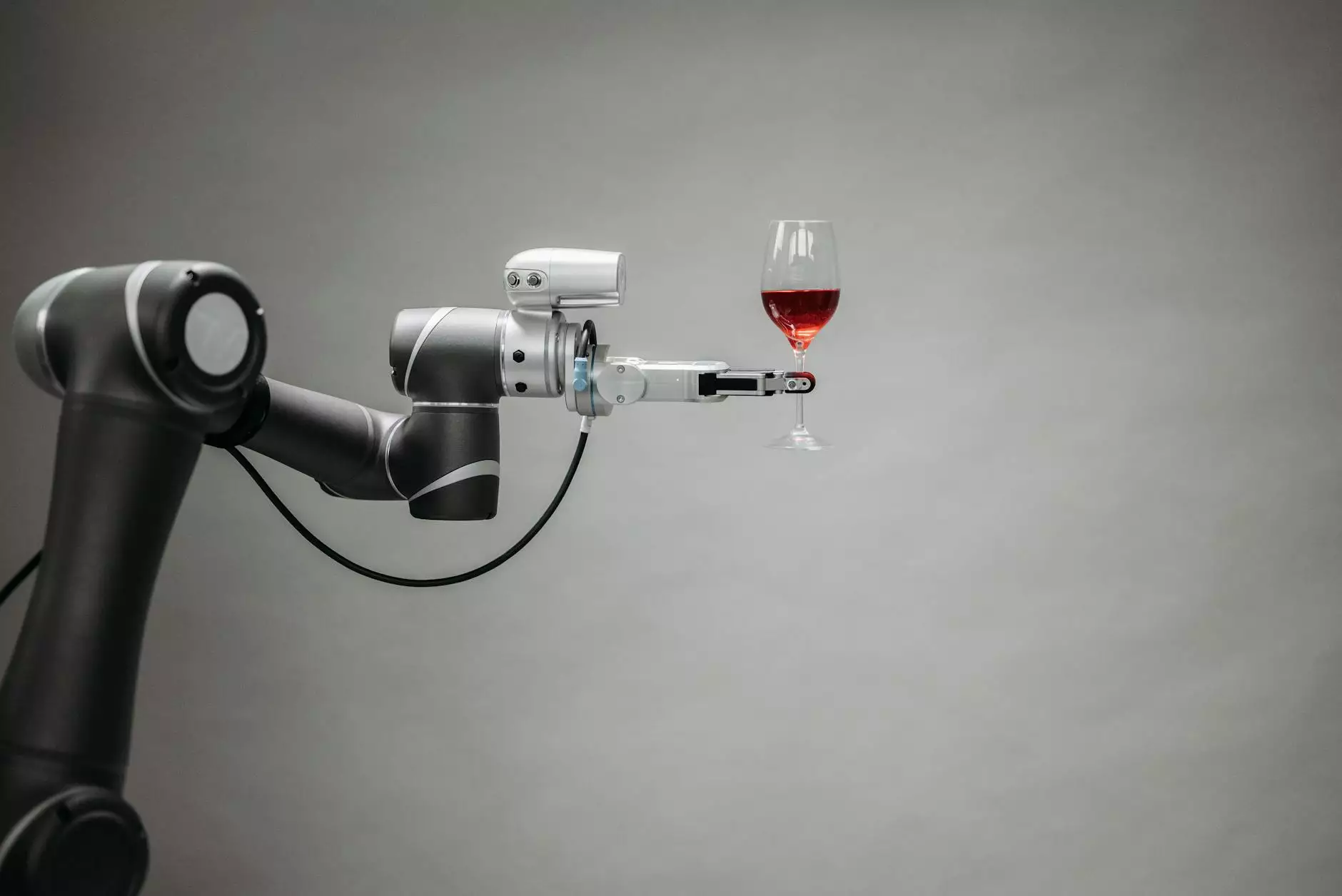
GRP composite housings are transforming the landscape of various industrial applications, providing significant advantages over traditional materials. These advanced materials are composed of glass-reinforced polymer (GRP), offering unparalleled performance in terms of durability, weight, and resistance to environmental factors.
The Rising Demand for GRP Composite Housings
In recent years, industries ranging from aerospace to marine engineering have experienced a surge in demand for GRP composite housings. As organizations seek to improve efficiency and reduce costs, the adoption of composite materials has become increasingly attractive. The properties of GRP make it an ideal candidate for applications that require robustness without the corresponding weight of metals or plastics.
Key Advantages of GRP Composite Housings
- Lightweight: One of the standout features of GRP composite housings is their lightweight nature. Weighing significantly less than steel, these housings allow for easier handling and installation.
- Corrosion Resistance: GRP is inherently resistant to many types of corrosion, making it an ideal choice for installations in harsh environments, such as coastal areas or chemical plants.
- Thermal Stability: GRP composite materials maintain their strength and integrity across a wide range of temperatures, which is crucial for industries dealing with extreme conditions.
- Customizable Designs: GRP composite housings can be easily molded into complex shapes, providing design flexibility that traditional materials cannot match.
- Low Maintenance: With their superior durability, GRP housings require minimal upkeep, significantly lowering maintenance costs over their lifetime.
Applications of GRP Composite Housings
The versatility of GRP composite housings is highlighted by their wide array of applications across many sectors. Below are some prominent industries leveraging the benefits of these innovative materials:
Aerospace Industry
In the aerospace sector, lightweight materials are critical for improving fuel efficiency. GRP composite housings are used in various components, including protective enclosures for electronic systems and structural parts, due to their lightweight and robust characteristics.
Marine Engineering
The marine industry utilizes GRP composite housings for a variety of applications, such as ship’s hulls, internal components, and electronics housing. The materials’ corrosion resistance and hydrophobic properties greatly extend the lifespan of marine constructions.
Electrical and Electronic Enclosures
Electrical industries benefit from the insulating properties of GRP composite housings. These materials provide excellent protection for electrical components against moisture and environmental factors, ensuring operational reliability.
Telecommunications
Telecommunication infrastructure often relies on GRP for protective enclosures due to their robustness and lightweight nature, enabling easier installation without compromising performance.
How Celtic Composites Leads the Market
At Celtic Composites, our expertise in GRP composite housings ensures that we provide cutting-edge solutions tailored to meet the unique demands of our clients. Our commitment to quality and innovation sets us apart in the composites industry.
Research and Development Focus
We continually invest in research and development to enhance our composite materials' performance and expand their applications. Our team of experts is dedicated to exploring new composite formulations that further improve durability and functionality.
Customer-Centric Solutions
Understanding our customers' specific needs is our priority. We focus on providing custom GRP composite housings that fit seamlessly into existing systems while ensuring maximum performance and reliability.
Eco-Friendly Alternatives with GRP Composite Housings
As organizations globally strive to reduce their carbon footprints, GRP composite housings present an eco-friendly alternative to conventional materials. The manufacturing processes of these composites often involve less energy and reduce waste. Furthermore, the longevity of GRP reduces the need for frequent replacements, contributing to less waste in landfills.
Sustainability Practices at Celtic Composites
We are committed to sustainable manufacturing practices at Celtic Composites. Our approach includes:
- Using recyclable materials whenever possible in our production processes.
- Implementing energy-efficient manufacturing methods.
- Promoting longevity in our designs to minimize environmental impact.
Industry Case Studies
Case Study 1: Aerospace Enhancement
In an innovative project, we collaborated with an aerospace manufacturer to design a GRP composite housing for aircraft instrumentation. The resulting product not only met the stringent weight requirements but also provided superior thermal insulation, enhancing the overall safety and performance of the aircraft.
Case Study 2: Marine Solutions
For a leading marine company, we developed GRP composite housings intended for underwater applications. The lightweight yet durable construction significantly improved the vessel's handling capabilities and reduced energy consumption.
Future Trends in GRP Composite Housings
The future of GRP composite housings appears promising as ongoing advancements in composite technology pave the way for even more innovative solutions. Industry trends indicate a focus on:
- Smart Composites: Incorporation of sensors and IoT technology into composite materials for real-time monitoring and enhanced performance.
- Advanced Manufacturing Techniques: Such as 3D printing, which could revolutionize how composite housings are produced, allowing for rapid prototyping and reduced waste.
- Sustainable Development: Continuous improvement in sustainable practices and materials to further decrease environmental impacts.
Conclusion
Overall, GRP composite housings present a revolutionary solution for a multitude of industries, offering an array of benefits from reduced weight and improved corrosion resistance to significant cost savings through minimal maintenance requirements. As a leader in this field, Celtic Composites remains dedicated to pushing the boundaries of what is possible with composite materials. Together, we can move towards a future where innovative materials redefine industry standards for performance and sustainability.