Unveiling the World of Die Casting Mold
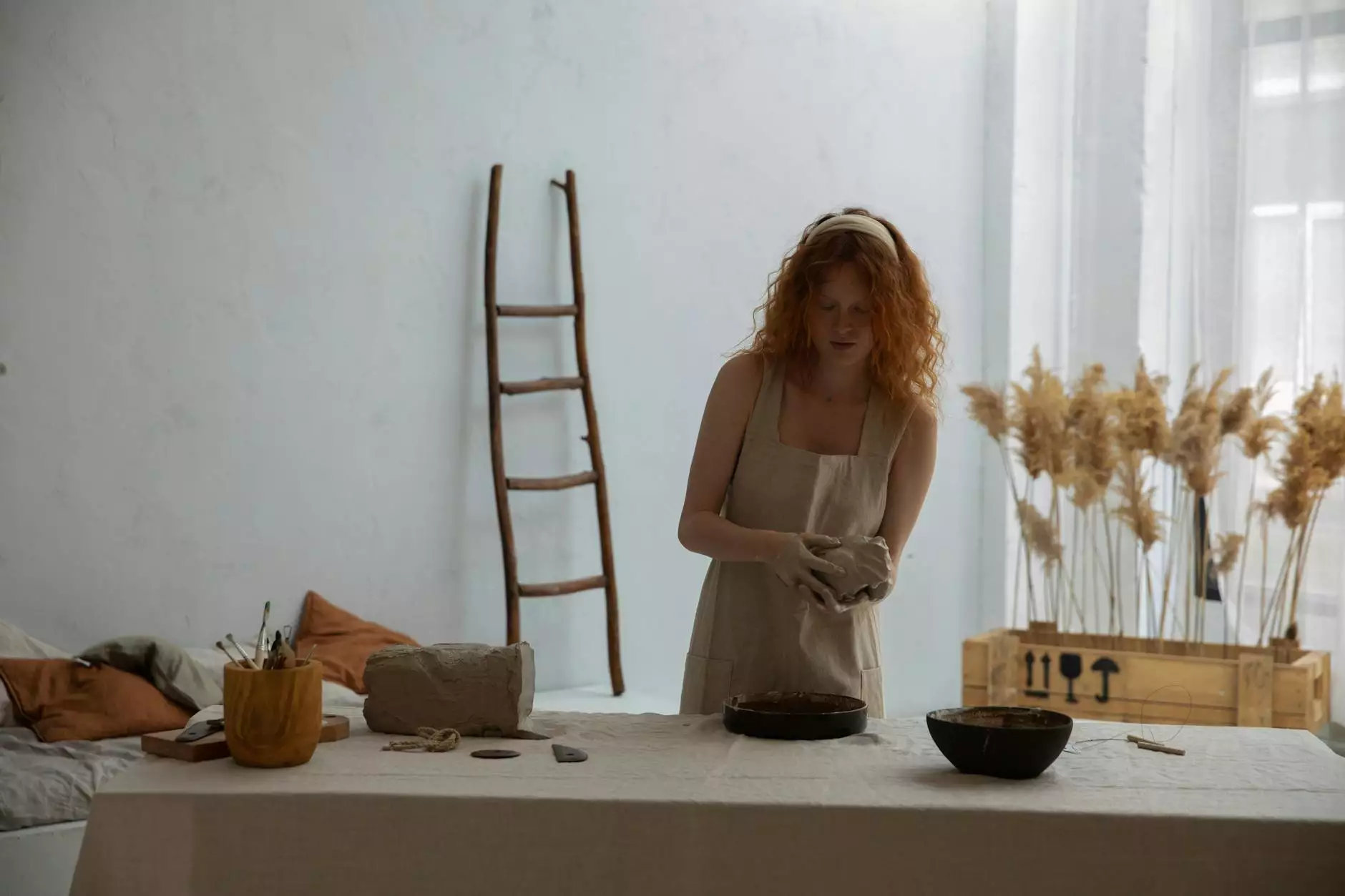
Die casting mold plays an instrumental role in the world of precision manufacturing, particularly within the realms of metal fabrication. As industries advance and demand for precision components surges, understanding the nuances of die casting molds can provide a competitive edge. In this detailed article, we will explore what die casting molds are, their significance, types, nuances, manufacturing processes, and various applications.
What is a Die Casting Mold?
At its core, a die casting mold is a specialized tooling used to create metal parts through the process of die casting. This involves forcing molten metal into a mold cavity under high pressure, allowing it to solidify and take the shape of the mold. The result is a component that is not only precise but also possesses excellent surface finish and exceptional dimensional accuracy.
Importance of Die Casting Mold in Metal Fabrication
- Precision Manufacturing: A well-engineered die casting mold is essential for producing high-quality components that meet strict tolerances.
- Cost Efficiency: Although the initial investment can be significant, die casting molds lead to lower production costs over time due to their durability and the speed of the manufacturing process.
- Versatility: Die casting can accommodate a wide range of materials, including zinc, aluminum, and magnesium, making it a versatile choice for various applications.
- Innovative Designs: Advanced die casting mold technologies allow for innovative designs that are complex and intricate.
Types of Die Casting Molds
Understanding the various types of die casting molds is essential for selecting the right one for specific applications. Here are the primary types:
1. Single Cavity Molds
These molds are designed to produce a single component per cycle. They are ideal for low-volume projects and prototyping, allowing for rapid testing of designs without the need for extensive tooling costs.
2. Multiple Cavity Molds
As the name suggests, multiple cavity molds can generate several identical parts in one cycle. This dramatically increases production efficiency and is suitable for high-volume manufacturing.
3. Family Molds
Family molds can produce different parts in one cycle, provided they are of similar geometry and material. This type of mold allows for flexibility in production, catering to varied product lines.
4. Combination Molds
Combination molds integrate both single cavity and multiple cavity designs, offering a balanced approach for various production requirements.
5. Cold Chamber Molds
Cold chamber die casting is primarily used with metals that have high melting points. In this process, the molten metal is poured into the chamber and then injected into the mold. It is particularly useful for aluminum and copper alloys.
6. Hot Chamber Molds
In contrast, hot chamber die casting uses a furnace that keeps the metal molten within the chamber, making it suitable for metals with lower melting points, such as zinc and lead.
The Die Casting Process
Executing precision in die casting involves several critical steps, each contributing to the quality of the end product:
Step 1: Mold Preparation
The die mold must be meticulously prepared to ensure a smooth production process. This includes applying a release agent to prevent the casting from sticking to the mold.
Step 2: Melting the Metal
Depending on the type of die casting involved, the chosen metal is heated to its melting point. In hot chamber die casting, this process occurs in the chamber itself, while in cold chamber die casting, it occurs separately and then transferred.
Step 3: Injection
Once the metal is molten, it is injected into the mold cavity at high pressure. This forces the material to fill every corner of the mold, ensuring that the final product is devoid of imperfections.
Step 4: Cooling
After injection, the molten metal needs time to cool and solidify. The cooling time will vary depending on the material and wall thickness of the component being manufactured.
Step 5: Ejection
Once the component is cooled, it is ejected from the die. This is where precision engineering ensures easy removal without damaging the casting.
Step 6: Finishing
After ejection, the component may undergo additional processes such as trimming, surface finishing, or machining to meet the required specifications.
Benefits of Using Die Casting Mold
Investing in high-quality die casting molds brings several advantages to metal fabrication:
- Improved Surface Finish: Die casting often results in a superior surface finish, eliminating much of the need for further polishing or treating.
- Enhanced Dimensional Stability: The high pressure used in the process ensures that parts maintain their shape and dimensions even under stress.
- Economical for Large Runs: While initial costs may be higher, the per-part cost decreases significantly for large production runs.
- Accelerated Production Rates: The speed of the die casting process allows for rapid production and quick turnaround times.
Applications of Die Casting Molds
Die casting molds find utility across various industries due to their capacity for precision and efficiency. Some common applications include:
- Automotive Industry: Components such as engine blocks, transmission cases, and various small parts.
- Aerospace: Lightweight yet strong components for aircraft and spacecraft.
- Electrical and Electronics: Housings and brackets for electrical devices, connectors, and heat sinks.
- Consumer Products: Kitchenware, tools, and decorative items that require intricate designs.
- Industrial Machinery: Components that demand high strength and precision.
Choosing the Right Die Casting Mold Manufacturer
Finding a reliable manufacturer can make a considerable difference in the performance and quality of die casting molds. Here are key factors to consider:
- Experience: Look for manufacturers with a track record of producing high-quality molds.
- Technological Capabilities: A modern facility equipped with the latest technology can significantly assure efficiency and precision.
- Customization: A reputable manufacturer should be able to offer customized solutions based on your specific requirements.
- Quality Assurance: Ensure they have stringent quality control processes to maintain product quality.
- Customer Support: A strong customer support system will assist with any queries or issues that arise during the production process.
Conclusion
The significance of die casting molds in the manufacturing sector cannot be overstated. They address the increasing demand for high-precision parts in numerous industries, promoting efficiency and cost-effectiveness in production processes. As a business, understanding the essentials of die casting molds will equip you with the knowledge to make informed decisions regarding your manufacturing needs.
For bespoke die casting solutions that prioritize quality and precision, consider partnering with Deep Mould. With a commitment to excellence in metal fabrication and a robust portfolio in die casting mold production, we are poised to help your business thrive.