How to Make Plastic Parts for Cars: A Comprehensive Guide
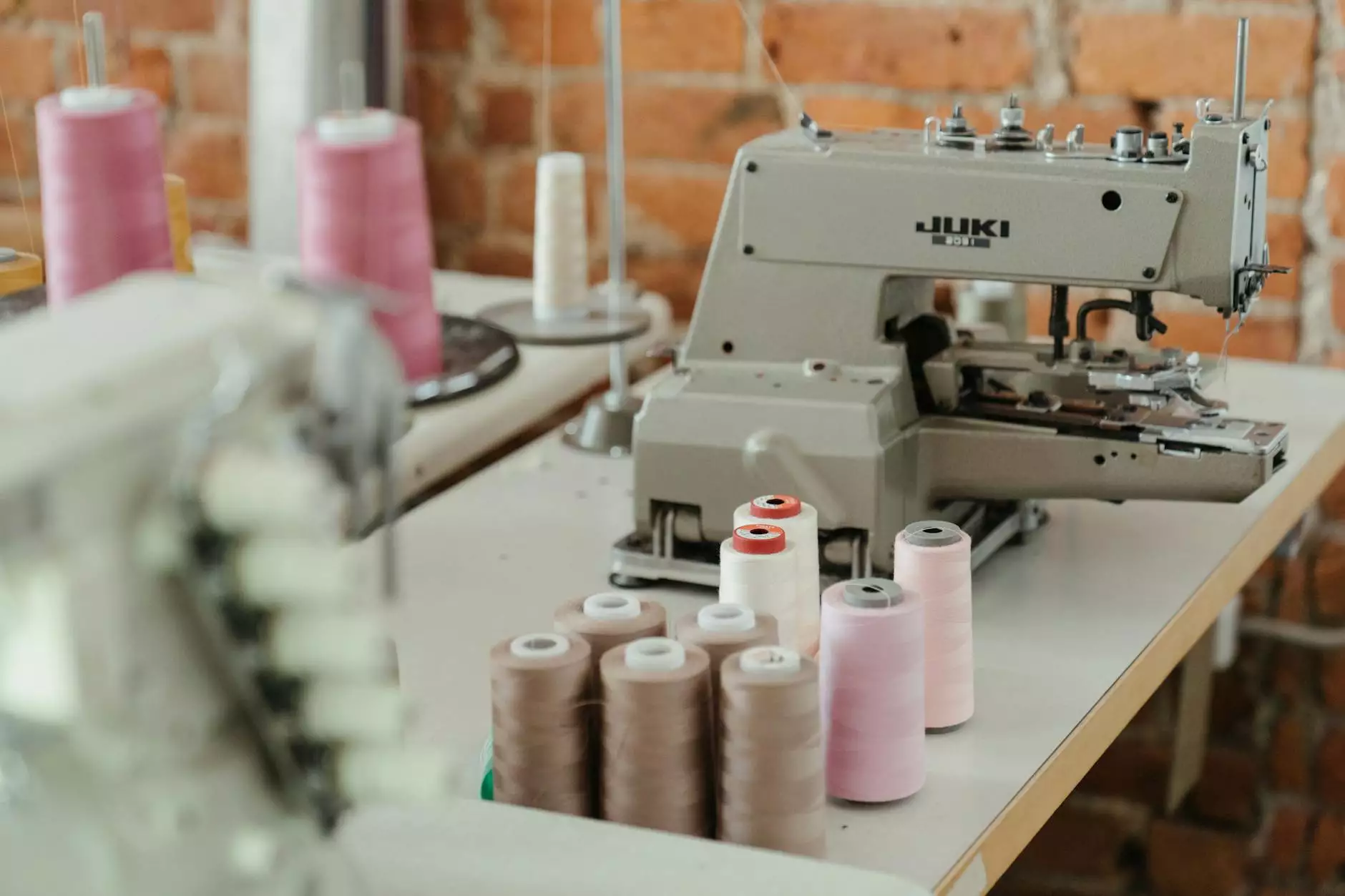
The automotive industry has witnessed remarkable advancements in the past few decades, with plastic parts becoming increasingly integral to vehicle design and functionality. Designing and manufacturing these components require expertise, precision, and an understanding of various molding techniques. In this article, we will explore how to make plastic parts for cars, focusing on the methods, materials, and best practices employed by professional manufacturers.
Understanding the Importance of Plastic Parts in Automotive Manufacturing
Plastic components have revolutionized the automotive sector. Their benefits include:
- Weight Reduction: Plastic is significantly lighter than metal, contributing to better fuel efficiency.
- Cost-Effectiveness: The production of plastic parts is often cheaper than that of metal components.
- Design Flexibility: Plastics can be molded into complex shapes, allowing for innovative designs.
- Corrosion Resistance: Unlike metal, plastic does not rust, enhancing the longevity of parts.
- Noise Reduction: Plastic parts often produce less noise than metal, contributing to a quieter ride.
Key Processes in Making Plastic Parts for Cars
Creating plastic parts involves several key processes. Here, we will discuss the most common techniques used in the production of automotive plastics.
1. Plastic Injection Molding
Injection molding is the most prevalent manufacturing process for producing plastic parts in the automotive industry. This method involves injecting molten plastic into a mold, where it cools and hardens into the desired shape. The steps involved are:
- Mold Design: Engineers design the mold based on specifications using CAD software.
- Mold Fabrication: The mold is then fabricated using high-precision CNC machines.
- Material Selection: A suitable plastic material is chosen, often polypropylene or ABS, based on performance requirements.
- Injection Process: The selected plastic is heated and injected into the mold under high pressure.
- Cooling: After a short period, the mold is cooled to solidify the plastic.
- Part Ejection: Once cooled, the mold opens, and the finished part is ejected.
- Finishing Touches: Additional processes like trimming, painting, or assembling are performed as needed.
2. Blow Molding
Blow molding is another method used for producing hollow plastic parts like fuel tanks or containers. The process involves:
- Material Preparation: Plastic is melted and formed into a parison, a tube-like structure.
- Blowing: The parison is placed in a mold and air is blown into it, expanding it to fit the mold.
- Cooling and Ejection: After cooling, the mold opens to release the finished part.
3. Thermoforming
Thermoforming is a simpler technique used for making large plastic sheets into specific shapes. The steps include:
- Material Heating: Sheets of plastic are heated until pliable.
- Mold Formation: The heated plastic is draped over a mold, and vacuum is applied to form the sheet into the desired shape.
- Trimming and Finishing: Once cooled, excess material is trimmed off, and additional finishing processes may be applied.
Materials Used in Making Plastic Parts for Cars
The choice of material is crucial in the production of plastic components for vehicles. Some common materials include:
- Polypropylene (PP): Known for its low density and impact resistance, it’s widely used for interior and exterior auto components.
- Acrylonitrile Butadiene Styrene (ABS): This material offers excellent toughness and heat resistance, making it ideal for parts like dashboards and wheel covers.
- Polycarbonate (PC): Renowned for its high impact resistance and optical clarity, it is often used in headlights and gauge lenses.
- Nylon (PA): Known for its strength and durability, nylon is commonly used for engine components and gears.
- Polyurethane (PU): This material is used for soft-touch applications such as seat covers and interior trim.
Quality Control in Plastic Part Manufacturing
Ensuring the quality of plastic parts is paramount, as substandard parts can lead to vehicle failures. Common quality control measures include:
- Material Testing: Raw materials are tested for properties like tensile strength and impact resistance before use.
- Dimensional Inspection: Automated measuring systems ensure that the produced parts meet the required specifications.
- Performance Testing: Parts undergo stress testing to ensure they can withstand operational conditions.
- Visual Inspections: Final products are inspected for defects such as surface blemishes and consistency.
Trends and Innovations in Automotive Plastic Manufacturing
The automotive industry is continuously evolving, and so are the innovations in plastic manufacturing. Some current trends include:
- Lightweight Materials: Manufacturers are exploring advanced composite materials to further reduce weight.
- Sustainable Plastics: The use of bio-based and recycled plastics is becoming more prevalent for environmental sustainability.
- 3D Printing: Additive manufacturing is being integrated for rapid prototyping and production of complex parts.
- Smart Plastics: Incorporating sensors and electronics into plastic components for advanced automotive applications.
Conclusion: The Role of Hanking Mould in Plastic Part Production
At hanking-mould.com, we specialize in the art and science of plastic molding, particularly in the automotive sector. Our extensive experience as a Plastic Mold Maker and Plastic Injection Mould Manufacturer allows us to serve the diverse needs of our clients effectively. Our commitment to quality, innovation, and customer satisfaction sets us apart in the competitive landscape of automotive manufacturing.
By understanding how to make plastic parts for cars, manufacturers can not only improve the efficiency of their production processes but also contribute to the evolution of automotive technology. From light-weighting components for better fuel efficiency to utilizing sustainable materials, the prospects for the future are exciting.
Partner with us to leverage state-of-the-art technology, exceptional craftsmanship, and a deep understanding of the industry to produce high-quality plastic parts that meet the demands of modern vehicles.